The Challenges of Drivetrain Performance Part 3 – The Opportunities & Future
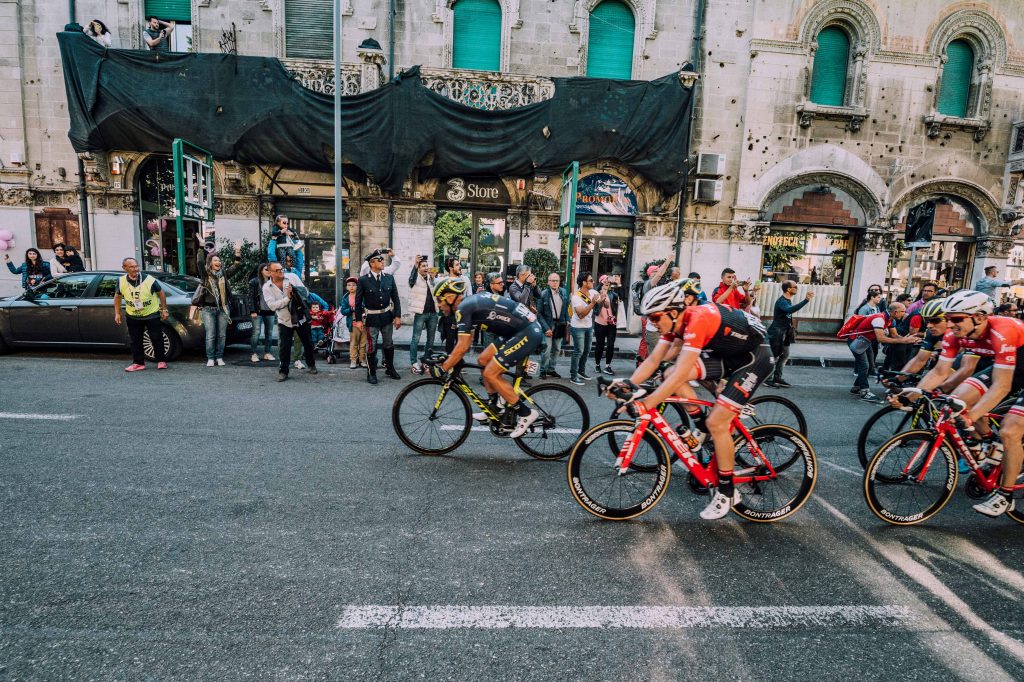
Part 3 – The opportunities & future
When we first presented our products and the performance gains available to the pro-teams one Performance Director commented that in their search for performance they have spent thousands of Euros in refining their rider positions so they are optimised for aero gains of less than 1%. The surprise for them was that the gains available in the transmission were so significant and that no one had challenged the current way of doing things up until now. What struck us about this was that if the best teams in the world are not aware of the opportunity for sizeable performance gains in the transmission, then it’s likely that no-one else would know either and so we would need to raise awareness of the extent to which a poorly maintained transmission can be encumbered with losses.
At Flaér we are approaching the problem from a different angle to the traditional chain lube manufacturers. Instead of trying to make sticky lubes that are difficult to wash away and end up collecting dirt, we have produced clean, non-sticky lubricants or fluids that are continually applied in micro-doses via a small on board reservoir whilst you ride. The result is that the dirt, grit and grime don’t stick as much and as the fluid is continually applied the fluid layer is being constantly topped up so even in the worst of conditions maximum performance is maintained all the time.
Future testing…..
In order to continue to understand the significant performance gains available in the drive chain we are always exploring new ways to improve the accuracy of our test data. Our work with Orica-Scott/Michelton-BikeExchange and the Cube Action Team supports our lab testing and gives real world feedback from riders at the highest levels in the sport. In addition to this we are also working on a number of other development projects, so watch this space!
Summary
Some key messages to take from this series: